A $10 billion construction project will change the future of energy
The task of getting clean, efficient energy created and distributed from Texas to the rest of the world is no small-or easy-task. And certainly not inexpensive. But the future of energy may well depend on the process of liquifying natural gas and shipping it out across the world. Natural gas can play an important immediate role as a transitional fuel (particularly in developing countries), helping phase out coal and thus immediately reducing CO2 emissions and air pollutants.
Texas produces more natural gas than any other state and more than twice as much as 48 of the other 49 states. Only Pennsylvania comes close to rivaling the natural gas production of Texas, which annually produces 7,993 billion cubic feet, accounting for 30 percent of America’s production.
One of the leading energy companies working to make this happen is Golden Pass LNG, which is three years into a five-year, $10 billion construction project to transform its existing import terminal in Sabine Pass, Texas, by adding liquefaction and export capabilities, providing flexibility to import and export natural gas in response to market conditions.
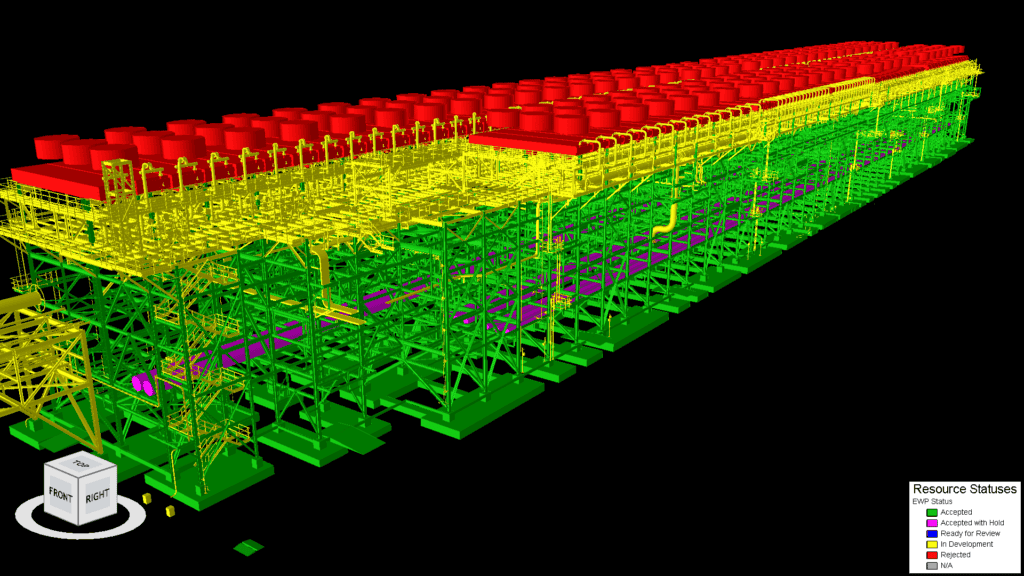
By digitalizing prior manual data entry and paper-based processes, Zachry Group saved 63,500 resource hours, which is equivalent to an average of five full-time resources, and reduced report generation time by 10 resource hours per week. Image courtesy of Zachry Group
The project includes three liquefaction process trains, each with an output of approximately 5.2 million tons per year, associated treatment, power, and utility systems as well as interconnections to existing import facilities and controls. It will use existing storage and pipeline infrastructure constructed for the company’s import terminal in Sabine Pass, about 75 miles east of Houston.
When the first liquefaction train comes online in 2024, Golden Pass will begin sending clean, affordable LNG from the Texas Gulf Coast to customers around the globe via the Sabine-Neches Waterway – one of the few deep-water ports along the Gulf Coast.
Golden Pass LNG is a 15-year-old LNG import terminal and pipeline company that became commercially operational in 2010, just when the market began its incredible transformation from energy shortage to energy abundance. The company vision is to become North America’s premier LNG export company and to supply clean energy from Texas to power the world.
The facility will have a total output capacity of 16 million metric tons of liquified natural gas (LNG) per year. Zachry Group, as part of an integral joint venture, was awarded the engineering, procurement, and construction contract to build the export facility.
The scope of work includes integrating and modifying existing state-of-the-art systems and equipment, and demands 6,000 to 7,000 on-site professionals at peak times, installation of more than 1.9 million feet of pipeline, more than 3,000 engineering work packages, and approximately 20,000 installation packages. Upon completion, the facility will generate billions of dollars in economic growth and connect natural resources with global markets, driving the client’s vision of becoming the premier LNG export company in North America.
Collaboration Challenges and Constraints
A truly global initiative, with an engineering team in Japan, fabrication occurring across 18 countries, and on-site construction in the U.S. Gulf Coast, the project presented coordination challenges, compounded by COVID-19 restrictions that significantly impacted travel and workflows. They had to coordinate thousands of team members and stakeholders.
Additionally, millions of pieces of equipment and materials sourced from global suppliers needed to be meticulously managed and stored within limited on-site laydown space. The sheer magnitude of the project, combined with the site constraints, required collaborative and cost-effective solutions to manage data, people, and processes both safely and effectively amid a worldwide pandemic.
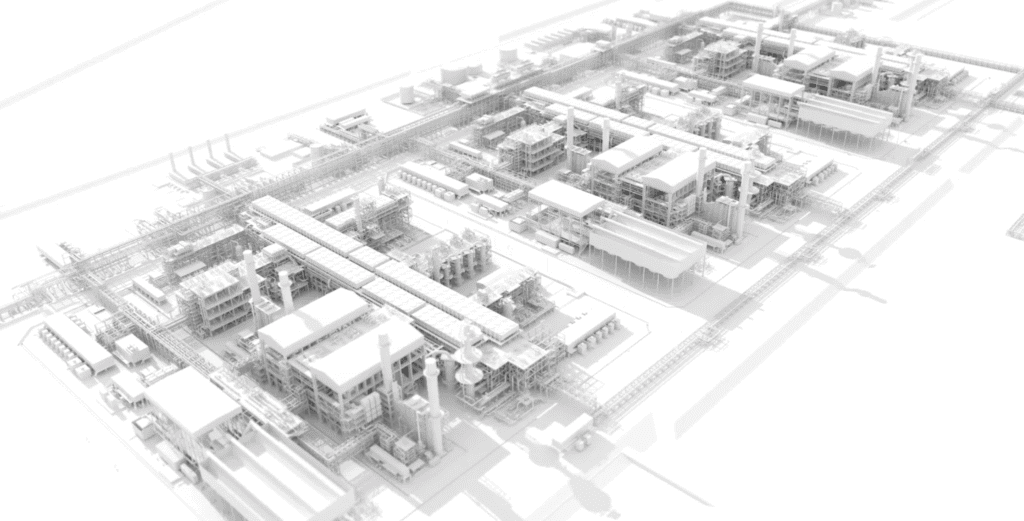
Golden Pass LNG is a $10 billion facility with a total output capacity of 16 million metric tons of liquified natural gas (LNG) per year. Zachry Group, as part of an integral joint venture, was awarded the engineering, procurement, and construction contract to build the export facility. Images courtesy of Zachry Group
To facilitate successful delivery of this large-scale project, Zachry sought to improve construction planning and work packaging, streamline workflows among the geographically dispersed teams, and provide visibility into the timing of material and equipment delivery to the site. In the past, they had used Gantt charts, spreadsheets, and PowerPoint presentations to manage and plan the construction processes and perform reviews. However, they realized that these manual, paper-laden methods were error-prone and lacked effective coordination and change management capabilities, often resulting in siloed information and schedule updates and status reports that were one to two weeks out of date. The massive project’s success hinged on establishing a connected, cloud-based digital data and construction planning environment.
“We would remove paper from the process and existing workflows where possible in order to improve productivity and enhance information transparency,” explained Jim Kinter, project IT/IM manager at Zachry Group.
Digitalizing Construction Planning and Workflows
For more than a decade, Zachry has used Bentley solutions and trusted their technology applications to deliver increased value throughout the design and construction lifecycle of their projects.
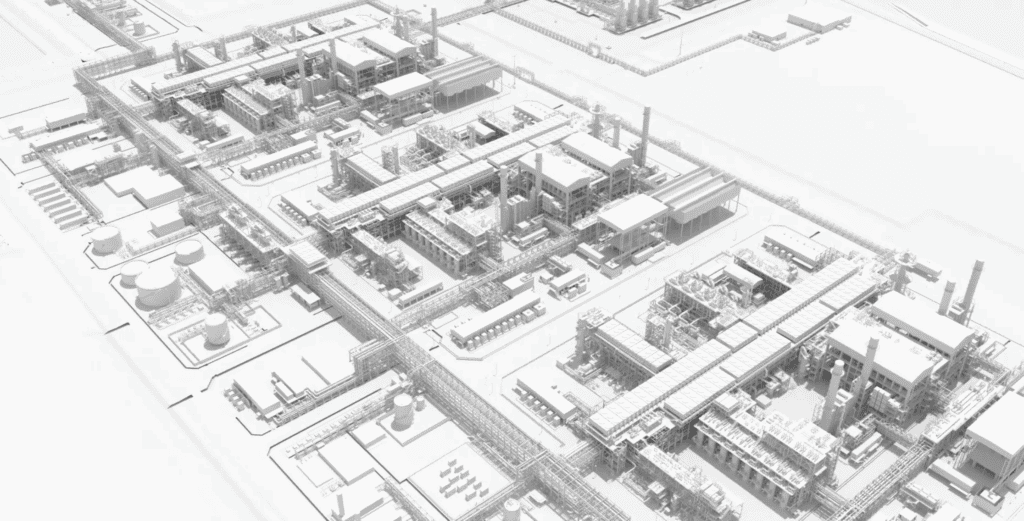
To facilitate successful delivery of this large-scale project, Zachry sought to improve construction planning and work packaging, streamline workflows among the geographically dispersed teams, and provide visibility into the timing of material and equipment deliveries to the site.
“Our strategic drivers [in going digital] were addressed by a portfolio of Bentley solutions, including SYNCHRO Pro, ConstructSim, and SYNCHRO Perform,” said Kinter. In the early stages of this project, Zachry completed a proof-of-concept for 4D planning using SYNCHRO Pro and integrated the 3D design model with the baseline schedule, providing a collaborative path of visual construction reviews for the entire team that proved invaluable.
“4D planning fundamentally changed the way the project team interacted with the schedule,” said Kinter. “What had taken months to prepare in a Gantt chart was validated and optimized in weeks [by] leveraging 4D planning.”
They implemented advanced digital work packaging using SYNCHRO and ConstructSim to facilitate and automate the development of construction and installation work packages. Integrating flexible daily cost capture features helped further extend modeling and digitalization capabilities to generate a comprehensive construction digital twin accessible to the entire project team. Working in a digital, cloud-based platform, the team could view and interact with the 4D model, regardless of location, eliminating the need to travel and supporting iterative and real-time model reviews. Using the digital model to perform schedule animation and clash detection, as well as dynamically visualize the laydown space, allowed the team to view the work and identify and mitigate risks prior to performing work on site.
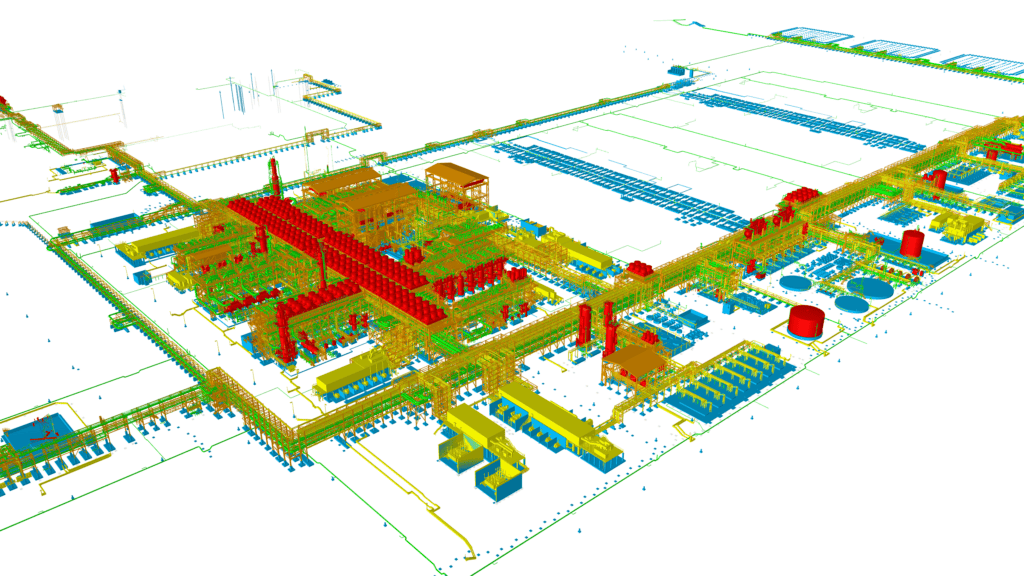
Zachry Group established a connected data environment, which ensured accurate reporting and provided trusted sources of information for the entire team. The result was a reduction in resource hours, increased productivity, cost savings, and improved safety conditions.
“With a global project team, and due to COVID-19 travel restrictions, our leadership team recognizes the value in deploying digital solutions that connect our team members, regardless of location,” explained Kinter. “Our team recognizes the value in leveraging 4D solutions to plan work activities in an optimized manner that reduces area congestion, and conduct work tasks that enable crews to identify and mitigate risks before stepping foot on site.”
Connected Digital Solutions
Leveraging Bentley’s applications, Zachry established a connected data environment, ensuring accurate reporting and providing trusted sources of information for the entire team. Working with interconnected data using integrated digital solutions automated workflows and enabled the team to communicate, collaborate, and leverage data in a visual environment for better planning and improved decision-making. As a result, they reduced resource hours, increased productivity, saved costs, and ensured safety.
Through the automation of work packaging, the team reduced the total amount of time required to create installation work packages from eight hours each to two hours each, achieving a 75 percent reduction in work package development time. Over the course of the project, this saved Zachry 120,000 resource hours. By digitalizing prior manual data entry and paper-based processes, they saved an additional 63,500 resource hours, equivalent to an average of five full-time resources, and reduced report generation time by 10 resource hours per week.
While many projects leverage 4D modeling solutions to support construction planning and execution, Zachry went a step further and established a construction digital twin during the design phase, demonstrating how Bentley solutions provide true value throughout the project lifecycle, from design through commissioning and facility start up.
The solution improved coordination among stakeholders amid a global pandemic, optimized the project schedule, and mitigated risks to workers.
“With a project of this size and magnitude, the only way to achieve success is by empowering team members to communicate, collaborate, and leverage data to make the right decisions at the right time through the use of [connected] digital solutions. The future of construction is digital,” said Kitner.
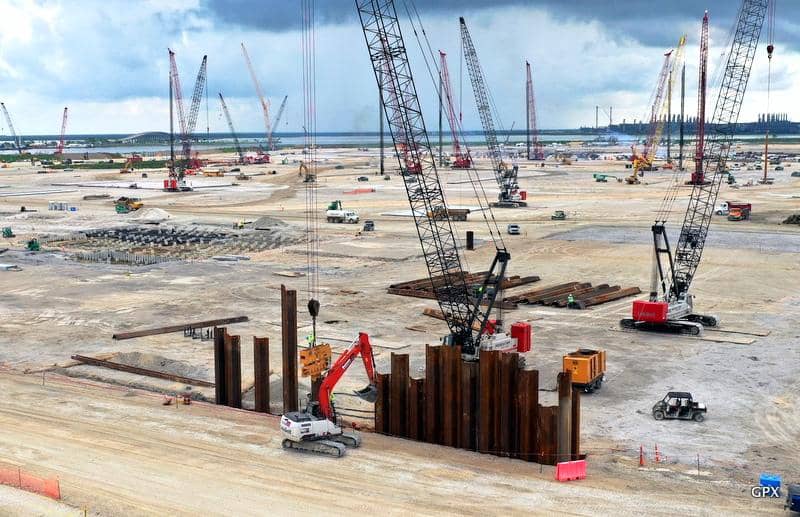
Golden Pass LNG under construction in Sabine Pass, Texas.